From Blueprint to Reality: The Michaels Sheet Metal Fabrication Process
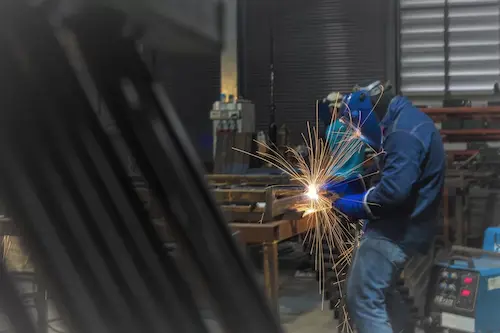
We take pride in our meticulous fabrication process, transforming blueprints into tangible metal products that stand the test of time.
Our approach is methodical, ensuring precision and quality at every stage.
This article provides an in-depth look into our fabrication process, detailing how we bring designs to life from the initial concept to the final product.
1. Initial Consultation and Blueprint Review
The journey begins with an initial consultation where we collaborate with our clients to understand their specific needs. During this phase, we review the blueprints or designs provided. Our team of experts meticulously examines every detail of the plans to ensure that they are comprehensive and feasible. We assess the design’s requirements, including dimensions, materials, and any special instructions, to prepare for the next steps.
2. Material Selection
Once we have a clear understanding of the project requirements, we proceed to material selection. We use a variety of high-quality metals, including stainless steel, aluminum, and copper. The choice of material depends on the project’s specifications and intended use. We ensure that all materials meet industry standards for strength, durability, and aesthetic appeal.
3. Detailed Fabrication Planning
With the blueprint and materials in hand, our team moves on to detailed fabrication planning. This step involves creating a detailed work plan that outlines each phase of the fabrication process. We use advanced software to create precise digital models of the components. These models help us identify potential challenges and plan for accurate cutting, shaping, and assembly.
4. Cutting and Shaping
The cutting and shaping phase is crucial in turning raw materials into the desired forms. We utilize state-of-the-art equipment such as CNC machines, laser cutters, and water jet cutters to achieve precise cuts. Our skilled technicians program these machines with the specifications from the digital models to ensure accuracy. We take great care during this phase to maintain the integrity of the material and achieve the exact dimensions required.
5. Forming and Bending
After cutting, the next step is forming and bending the metal components. This process involves shaping the metal into curves, angles, and other complex forms as specified in the blueprints. We employ various techniques, including hydraulic press brakes and roll formers, to achieve the desired shapes. Our team constantly monitors the process to ensure that each component meets the required tolerances and specifications.
Get Started
For any questions or concerns, get in touch with our knowledgeable staff today. We would be glad to assist you!
Contact Us Today6. Welding and Assembly
Once the components are shaped, they are ready for welding and assembly. Our skilled welders use advanced welding techniques to join the components together. This phase is critical for ensuring the structural integrity of the final product. We use MIG, TIG, and spot welding methods, depending on the material and design requirements. Each weld is inspected for strength and quality to ensure that the final product is robust and reliable.
7. Surface Finishing
Surface finishing is the next step in our fabrication process. This phase involves cleaning, polishing, and coating the metal components to enhance their appearance and protect them from corrosion. We offer a range of finishing options, including powder coating, anodizing, and plating. The choice of finish depends on the project’s aesthetic and functional requirements. Our team ensures that each finish is applied evenly and meets the highest standards of quality.
8. Quality Control and Testing
At Michaels Sheet Metal, quality control is integral to our fabrication process. Before the final product leaves our facility, it undergoes rigorous testing and inspection. We check for adherence to the specifications outlined in the blueprints, ensuring that all dimensions, shapes, and finishes are accurate. We also perform functional tests to verify that the components meet performance standards. Any discrepancies are addressed promptly to ensure that the final product meets our high standards of quality.
9. Packaging and Delivery
Once the quality control checks are complete, we prepare the components for packaging and delivery. We carefully package each item to protect it during transportation. Our packaging process is designed to prevent damage and ensure that the components arrive at their destination in pristine condition. We coordinate with logistics partners to schedule timely delivery and ensure that the products reach our clients as expected.
10. Client Feedback and Adjustments
After delivery, we value client feedback to ensure satisfaction with the final product. We are committed to continuous improvement and are always open to making adjustments based on client input. If any modifications are required, we address them promptly to ensure that the final outcome aligns with the client’s vision and requirements.
At Michaels Sheet Metal, our fabrication process is designed to turn blueprints into high-quality metal products with precision and efficiency. From the initial consultation to the final delivery, we are dedicated to maintaining the highest standards of quality and craftsmanship. Our detailed approach ensures that every project meets our clients’ specifications and exceeds their expectations.