Custom Sheet metal fabrication in los angeles is a trade that has been around for decades. The industry has evolved with the emergence of new technologies, and we are seeing a new explosion of innovation in design and engineering. More than ever, companies are looking to their metal fabricator to turn ideas into reality. “Metal Fabrication” has become an art form, especially in this new engineering world. The metal fabricator is often the linchpin between mechanical and design engineering, delivering high-quality products on time and budget.
Why Choose Michaels Sheet Metal for Your Custom Metal Fabrication Requirements?
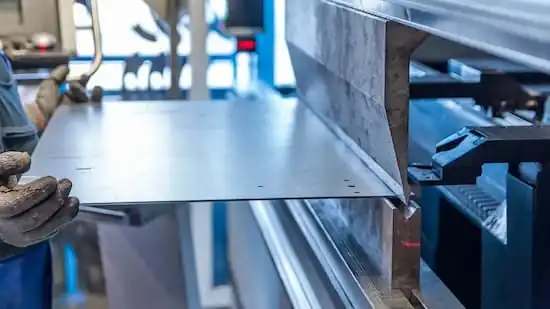
Michaels Sheet Metal specializes in diverse fabrication projects. Our experienced staff will help you develop your ideas into reality by connecting you with the resources necessary to realize them. We can often bring your idea from the drawing board to a finished product quickly and with exceptional quality. Michaels Sheet Metal has experience in diverse materials, including steel and aluminium.
Custom metal fabrication is a trade that uses raw materials to fabricate complex assemblies or parts. Metal fabrication involves many different disciplines, including welding, cutting, machining, and joining by adhesives. The trade often involves designer and engineer input and a crew of skilled production workers. The end product is often a one-off design or, in some cases, a very limited production run.
The fabrication method often defines custom metal fabrication, with many specialties in each field. Cutters are constantly modifying parts to meet production demands at high volume. The role of the metal fabricator in this process is to master new technologies and train and develop new skills within the workforce to meet these demands. To do this, they must constantly advance their knowledge and training and seek technological innovation. Custom metal fabrication of sheet metals and flat panels is a common trade. This can include items made by traditional methods, such as sheet metal bending and forming. In this field, the metal fabricator has to master all shop tools, including shear, brake, punches, and power saws.
Uses of Sheet Metal Fabrication in Brentwood
Sheet metal fabrication produces complex shapes and components from metal sheets. It involves cutting, bending, and forming metals into various shapes and sizes. The methods used will vary depending on the specific application. In this case, the metal will be cut using subtractive cutting techniques. This includes water jet cutting, laser cutters, and plasma cutters. Advanced computer-controlled machines are used to make increasingly intricate parts in shorter production runs. The shape and geometry of the part are key. The cutting will be made to a tolerance of plus or minus 1/1000th of an inch. In short, complex pieces of metal will be cut and compiled into 100s of parts to solve a single problem. The result is to build complex shapes and components with the highest level of precision possible.
Cutting involves removing material from the base to create a new shape or separate one part from another. Many cutting methods are available, but the most common include sawing and sanding. The choice of cutting method will depend on the specific application and desired results. For example, sawing is a great way to cut metal when you need to remove large amounts of material for a single piece. On the other hand, sanding can create complex shapes and has a much finer tolerance. It is best for making long cuts with very detailed edges and shapes. Sheet metal fabrication will often use a combination of methods depending on the job.
Process for Custom Sheet Metal Fabrication
Welding is fastening pieces of metal by melting them or fusing them with an inert filler material. The resulting bond is often stronger than the base material. The weld can also be used as a form of decoration or as a way to obtain specific properties such as color or pattern. It is an essential component in many different industries and is used in nearly all metal fabrication processes. Sheet metal fabrication is no different. The weld production is often automated, requiring specialized equipment and the right amount of filler material. It is a very precise process, requiring an operator to have a strong basic understanding of welding.
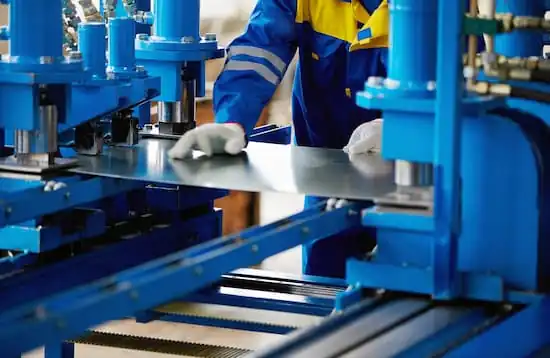
Sheet metal fabrication involves creating parts with specific dimensions that might not be possible with other methods. For example, you might have an idea for a new product but need it to be even thinner than normal. This is where deformation can come in handy. The most common way to deform metal is through rolling or bending. This can be performed manually or using a specialized piece of equipment. For example, you may pass the part through a series of rollers, each slightly smaller than the previous one. This will deform the metal as it passes through. Next, the part is bent and held in place by clamps or bolts. The piece is then allowed to cool. This will become a hardened solid structure that can be cut and formed into the final shape.
The deformation process is not limited to just bending, and you can also use it to create slots, holes, or any other desired feature. The part might deform a certain way and then be bent in another place to make the final product look right.
Do Not Hesitate To Reach Out to Michaels Sheet Metal To Learn More About Custom Metal Sheet Fabrication in Los Angeles.
We look forward to speaking with you and helping you develop your product or project for custom metal sheet fabrication. Michaels Sheet Metal is committed to providing you with all the necessary materials and expert guidance to bring your vision to life. Custom Sheet Metal Fabrication services are available in Beverly Hills, Santa Monica, Brentwood, Encino, Tarzana and Malibu