Step-by-Step Guide to Fabricating Durable Sheet Metal Door Pans
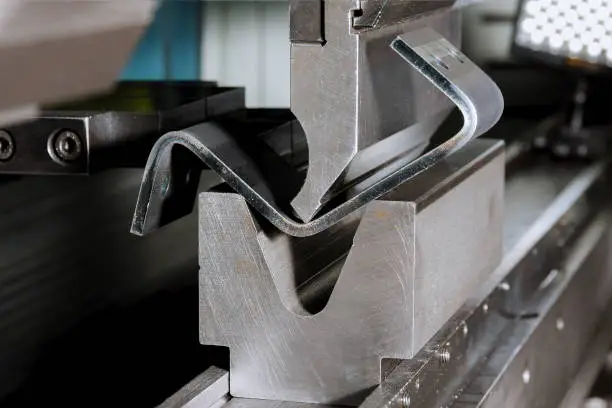
Fabrication requires expertise, attention to detail, and the right equipment to ensure strength and longevity.
This guide outlines the essential steps in fabricating durable sheet metal door pans, highlighting best practices and key considerations.
1. Selecting the Right Material
The foundation of a durable sheet metal door pan starts with choosing the appropriate material. Common options include:
- Stainless Steel – Offers excellent corrosion resistance and durability.
- Galvanized Steel – Provides a protective zinc coating to prevent rust.
- Aluminum – Lightweight and corrosion-resistant, making it ideal for various applications.
- Cold-Rolled Steel – Provides superior strength and a smooth finish, perfect for indoor applications.
Material selection depends on environmental conditions, load-bearing requirements, and aesthetic preferences. At Michaels Sheet Metal, we assess project specifications to recommend the best material for optimal performance.
2. Measuring and Cutting the Metal
Precision cutting is crucial for ensuring an exact fit. This step involves:
- Measuring the required dimensions using calipers, rulers, and digital measuring tools.
- Marking the cut lines clearly to prevent errors.
- Cutting the sheet metal using advanced tools such as shears, laser cutters, or plasma cutters.
Accuracy at this stage reduces material waste and ensures consistency across multiple door pans.
3. Forming and Shaping
After cutting, the sheet metal must be bent or shaped to match the design specifications. Key techniques include:
- Brake Press Forming – Utilizes a press brake to create precise bends at required angles.
- Roll Forming – Rollers bend the metal gradually into the desired shape.
- Hydraulic Pressing – Applies controlled pressure for complex shapes.
The choice of forming method depends on the design complexity and material thickness. At Michaels Sheet Metal, we use state-of-the-art equipment to ensure high accuracy in shaping door pans.
4. Welding and Joining
For added strength, the metal components are welded or joined. This step involves:
- TIG (Tungsten Inert Gas) Welding – Produces clean and precise welds, ideal for stainless steel and aluminum.
- MIG (Metal Inert Gas) Welding – Suitable for thicker metals, offering strong and durable joints.
- Spot Welding – Used for assembling thin sheet metal pieces without excessive heat distortion.
- Riveting or Fastening – An alternative to welding, depending on the application.
Proper welding techniques ensure the structural integrity of the sheet metal door pans, preventing weak points or deformities.
5. Surface Treatment and Finishing
The finishing process enhances durability and aesthetics. Key finishing techniques include:
- Deburring – Removes sharp edges and burrs for a smooth finish.
- Powder Coating – Provides a durable, corrosion-resistant finish.
- Galvanization – Adds a protective zinc layer to steel for rust resistance.
- Anodizing – Strengthens aluminum and enhances its appearance.
- Painting or Plating – Adds an extra layer of protection and aesthetic appeal.
The choice of finishing method depends on the door pan’s environmental exposure and design requirements.
6. Quality Inspection and Testing
At Michaels Sheet Metal, every fabricated door pan undergoes rigorous quality checks to meet industry standards. The inspection process includes:
- Dimensional Accuracy Check – Ensures all measurements align with specifications.
- Strength and Durability Testing – Confirms the pan can withstand expected loads and conditions.
- Surface Defect Inspection – Identifies and rectifies any imperfections.
- Corrosion Resistance Testing – Ensures the finish provides adequate protection.
By maintaining strict quality control, we guarantee that each sheet metal door pan meets performance expectations.
7. Packaging and Delivery
Proper packaging prevents damage during transportation. This step includes:
- Protective Wrapping – Using foam, plastic films, or corrugated sheets to prevent scratches.
- Custom Crating – For large or heavy door pans requiring additional support.
- Labeling and Documentation – Ensuring easy identification and handling.
Michaels Sheet Metal ensures secure and efficient delivery, minimizing the risk of transit damage.
8. Installation Considerations
Proper installation ensures longevity and functionality once the sheet metal door pan reaches its destination. Key factors include:
- Correct Alignment – Ensuring the pan fits perfectly within the door frame.
- Secure Fastening – Using appropriate screws, rivets, or adhesives for a firm hold.
- Sealant Application – Preventing moisture penetration and enhancing durability.
Michaels Sheet Metal guides best installation practices to maximize the lifespan of the fabricated door pans.
Final Thoughts
Fabricating durable sheet metal door pans requires precision, expertise, and high-quality materials. At Michaels Sheet Metal, we meticulously ensure each door pan meets industry standards for strength, durability, and aesthetics.
Need precision-crafted sheet metal door pans? Contact Michaels Sheet Metal for expert fabrication services today!