Precision Engineering: How Custom Sheet Metal Fabrication Enhances Your Projects.
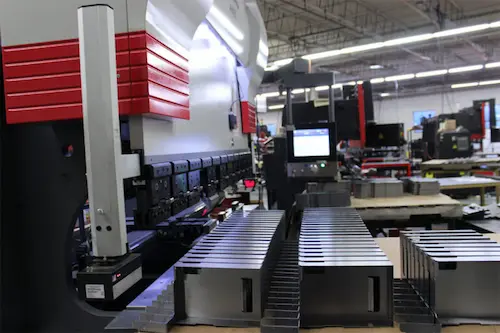
We are committed to delivering precision-engineered solutions through our custom sheet metal fabrication services. Understanding the lifecycle of custom sheet metal fabrication is essential to appreciating the intricate processes and ensuring the highest quality outcomes.
Our goal is to educate our clients and partners about each stage, from conceptualization to final production, ensuring transparency and fostering confidence in our expertise.
1. Conceptualization and Design
The lifecycle of custom sheet metal fabrication begins with the conceptualization and design phase. During this initial stage, our team at Michaels Sheet Metal works closely with clients to understand their specific requirements, including dimensions, material preferences, and functional needs. We employ advanced CAD (Computer-Aided Design) software to create precise digital models of the components. This design phase is crucial, as it sets the foundation for all subsequent processes.
In this phase, our designers focus on the functionality and aesthetic aspects of the project. We ensure that the design adheres to industry standards and client specifications. Collaboration between our designers and clients helps identify potential challenges early and refine the design to meet all functional requirements.
2. Material Selection
Once the design is finalized, we proceed to the material selection phase. Michaels Sheet Metal offers a variety of sheet metal materials, including steel, aluminum, copper, and stainless steel. Each material has unique properties that influence the fabrication process and the final product’s performance.
Selecting the appropriate material is crucial for achieving the desired strength, durability, and appearance. Our team provides expert guidance to help clients choose the best material based on their project’s requirements, environmental conditions, and budget constraints.
3. Cutting and Shaping
With the design and material in place, we move to the cutting and shaping phase. We utilize state-of-the-art cutting technologies such as laser cutting, waterjet cutting, and CNC (Computer Numerical Control) punching. These methods ensure high precision and efficiency in shaping the metal sheets according to the design specifications.
Laser cutting is particularly effective for intricate designs and thin materials, while waterjet cutting is ideal for thicker materials and more complex shapes. CNC punching provides flexibility for producing repetitive patterns and standard shapes. Each cutting method is chosen based on the project’s needs to ensure accuracy and quality.
4. Forming and Bending
After cutting, the metal sheets undergo forming and bending to achieve the desired shapes. This phase involves using various machinery such as press brakes and roll formers to create the necessary angles and curves. We pay meticulous attention to detail during this phase to ensure that each component matches the design specifications precisely.
Forming and bending are critical processes that influence the final product’s fit and functionality. Our skilled technicians employ advanced techniques to handle complex geometries and ensure that the metal components meet the required tolerances.
5. Welding and Assembly
Following the forming and bending stage, we move to welding and assembly. This phase involves joining multiple metal pieces together to create the final component or assembly. We utilize various welding techniques, including MIG (Metal Inert Gas) welding, TIG (Tungsten Inert Gas) welding, and spot welding, depending on the material and project requirements.
Welding requires precision and expertise to ensure strong, clean welds that meet structural and aesthetic standards. Our team performs rigorous quality checks throughout the welding process to ensure that all joints are secure and free of defects.
6. Surface Treatment and Finishing
Surface treatment and finishing are the final stages of the custom sheet metal fabrication lifecycle. This phase involves applying various treatments to enhance the appearance, durability, and functionality of the metal components. Common treatments include powder coating, anodizing, and plating.
Powder coating provides a durable, attractive finish that protects against corrosion and wear. Anodizing, typically used for aluminum, creates a protective layer that enhances corrosion resistance and appearance. Plating, such as zinc or chrome plating, adds a protective layer to the metal surface.
We offer a range of finishing options to meet client preferences and project requirements. Our team ensures that each component receives the appropriate treatment to achieve the desired look and performance.
7. Quality Control and Testing
Quality control and testing are integral parts of our fabrication process. We implement stringent quality control measures at every stage of the lifecycle. Our team conducts thorough inspections to ensure that each component meets the design specifications and industry standards.
Testing may include dimensional checks, visual inspections, and functional tests to verify that the components perform as expected. We also employ advanced measuring tools and techniques to ensure precision and consistency throughout the fabrication process.
8. Delivery and Installation
Once the fabrication and quality control processes are complete, we proceed to delivery and installation. Michaels Sheet Metal coordinates the logistics of transporting the finished components to the client’s location. Our team ensures that the components are carefully packaged and handled to prevent damage during transit.
For projects requiring installation, our skilled technicians are available to perform on-site assembly and installation. We ensure that all components are installed correctly and function as intended, providing a seamless transition from fabrication to final use.
9. Post-Installation Support
At Michaels Sheet Metal, our commitment to excellence extends beyond the completion of the project. We offer post-installation support to address any questions or concerns that may arise. Our team is available to provide maintenance recommendations, troubleshooting assistance, and any necessary adjustments to ensure the continued performance and satisfaction of our clients.
Understanding the custom sheet metal fabrication lifecycle is essential for appreciating the precision and care involved in delivering high-quality products. We are dedicated to providing exceptional service and expertise throughout every stage of the fabrication process, ensuring that our clients receive the best possible outcomes for their projects.